Use lots to manage groups of products¶
Lots are one of the two ways to identify and track products in Odoo. A lot usually indicates a specific batch of an item that was received, is currently stored, or was shipped from a warehouse, but can also pertain to a batch of products manufactured in-house, as well.
Manufacturers assign lot numbers to groups of products that have common properties; this can lead to multiple goods sharing the same lot number. This helps to identify a number of products in a single group, and allows for end-to-end traceability of these products through each step in their lifecycles.
Lots are useful for products that are manufactured or received in large quantities (such as clothes or food), and can be used to trace a product back to a group. This is especially useful when managing product recalls or expiration dates.
Enable lots & serial numbers¶
To track products using lots, the Lots & Serial Numbers feature must be enabled. Go to the Traceability section, and click the box next to Lots & Serial Numbers. Then, click the Save button to save changes.
, scroll down to the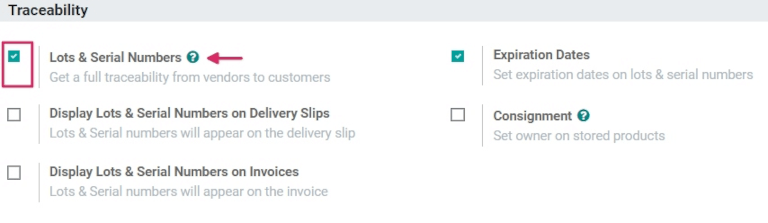
Track products by lots¶
Once the Lots & Serial Numbers setting has been activated, individual products can now be configured to be tracked using lots. To do this, go to the , and choose a product.
Once on the product form, click Edit to make changes to the form. Then, click the Inventory tab. In the Traceability section, click By Lots. Then, click Save to save changes. Existing or new lot numbers can now be assigned to newly-received or manufactured batches of this product.
Important
If a product has stock on-hand prior to activating tracking by lots or serial numbers, an inventory adjustment might need to be performed to assign lot numbers to the existing stock.
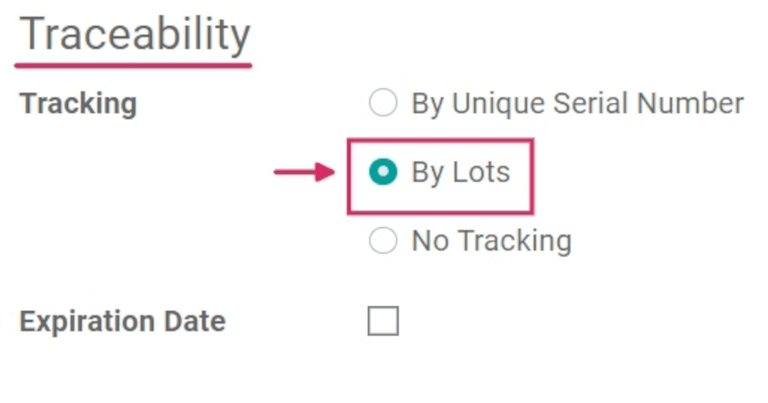
Create new lots for products already in stock¶
New lots can be created for products already in stock with no assigned lot number. To do this, go to the Create. Doing so reveals a separate page where a new Lot/Serial Number is generated automatically.
, and clickTip
While Odoo automatically generates a new Lot/Serial Number to follow the most recent number, it can be edited and changed to any desired number, by clicking the line under the Lot/Serial Number field, and changing the generated number.
Once the new Lot/Serial Number is generated, click the blank field next to Product to reveal a drop-down menu. From this menu, select the product to which this new number will be assigned.
This form also provides the option to adjust the Quantity, assign a unique Internal Reference number (for traceability purposes), and assign this specific lot or serial number configuration to a specific website in the Website field (if working in a multi-website environment).
A detailed description of this specific lot or serial number can also be added in the Description tab below.
When all desired configurations are complete, click the Save button to save all changes.
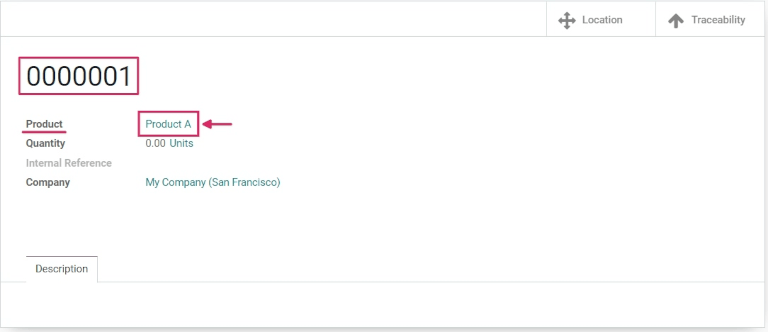
After a new lot number has been created, saved, and assigned to the desired product, navigate back to the product form in the
app, by going to , and selecting the product to which this newly-created lot number was just assigned.On that product’s detail form, click the Lot/Serial Numbers smart button to view the new lot number. When additional quantity of this product is received or manufactured, this new lot number can be selected and assigned to it.
Manage lots for shipping and receiving¶
Lot numbers can be assigned for both incoming and outgoing goods. For incoming goods, lot numbers are assigned directly on the purchase order form. For outgoing goods, lot numbers are assigned directly on the sales order form.
Manage lots on receipts¶
Assigning lot numbers to incoming goods can be done directly from the purchase order (PO).
To create a PO, go to
. Doing so reveals a new, blank request for quotation (RFQ) form.On this RFQ, fill out the necessary information by adding a Vendor, and adding the desired products to the Product lines, by clicking Add a product (under the Products tab).
Choose the desired quantity of the product to order by changing the number in the Quantity column.
Once the RFQ has been filled out, click Confirm Order. When the RFQ is confirmed, it becomes a Purchase Order, and a Receipt smart button appears. Click the Receipt smart button to be taken to the warehouse receipt form.
Note
Clicking Validate before assigning a lot number to the ordered product quantities will result in a User Error pop-up. The pop-up requires entry of a lot or serial number for the ordered products. The RFQ cannot be validated without a lot number being assigned.
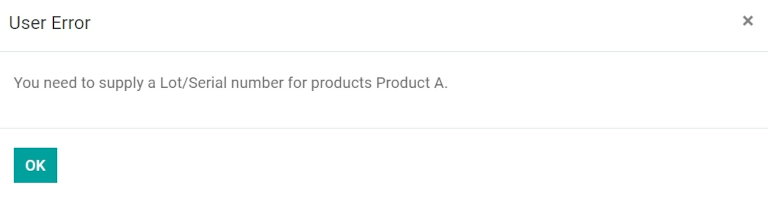
From here, click the Additional Options menu, represented by a hamburger (four horizontal lines) icon, located to the right of the Unit of Measure column in the Operations tab). Clicking that icon reveals a Detailed Operations pop-up.
In this pop-up, configure a number of different fields, including the assignation of a lot number, under the Lot/Serial Number Name column, located at the bottom of the pop-up.
There are two ways to assign lot numbers: manually and copy/paste.
Manually assign lot numbers: Click Add a line and choose the location the products will be stored in under the To column. Then, type a new Lot Number Name and set the Done quantity.
Note
If quantities should be processed in multiple locations and lots, click Add a line and type a new Lot Number Name for additional quantities. Repeat until the Quantity Done matches the Demand.
Copy/paste lot numbers from a spreadsheet: Populate a spreadsheet with all of the lot numbers received from the supplier (or manually chosen to assign upon receipt). Then, copy and paste them in the Lot/Serial Number Name column. Odoo will automatically create the necessary number of lines based on the amount of numbers pasted in the column. From here, the To locations and Done quantities can be manually entered in each of the lot number lines.
Once all product quantities have been assigned a lot number, click Confirm to close the pop-up. Then, click Validate.
A Traceability smart button appears upon validating the receipt. Click the Traceability smart button to see the updated Traceability Report, which includes: a Reference document, the Product being traced, the Lot/Serial # assigned, and more.
Manage lots on delivery orders¶
Assigning lot numbers to outgoing goods can be done directly from the sales order (SO).
To create an SO, go to the
. Doing so reveals a new, blank quotation form.On this blank quotation form, fill out the necessary information by adding a Customer, and adding products to the Product lines (in the Order Lines tab) by clicking Add a product.
Then, choose the desired quantity to sell by changing the number in the Quantity column.
Once the quotation has been filled out, click the Confirm button to confirm the quotation. When the quotation is confirmed, it becomes an SO, and a Delivery smart button appears.
Click the Delivery smart button to view the warehouse receipt form for that specific SO.
From here, click the Additional Options menu, represented by a hamburger
icon (four
horizontal lines, located to the right of the Unit of Measure column in the
Operations tab). Clicking that icon reveals a Detailed Operations pop-up.
In the pop-up, a Lot/Serial Number will be chosen by default, with the full Reserved quantity taken from that specific lot (if there is enough stock in that particular lot).
If there is insufficient stock in that lot, or if partial quantities of the Demand should be taken from multiple lots, change the quantity in the Done column to only include that specific part of the total quantity.
Note
The lot automatically chosen for delivery orders varies, depending on the selected removal strategy (FIFO, LIFO, or FEFO). It will also depend on the quantity ordered, and if there is enough quantity in one lot to fulfill the order.
See also
Then, click Add a line, select an additional (different) Lot/Serial Number, apply the rest of the Done quantities, and click Confirm to close the pop-up. Lastly, click the Validate button to deliver the products.
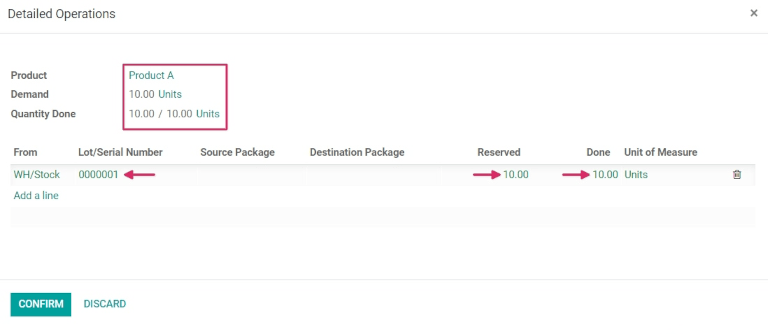
Upon validating the delivery order, a Traceability smart button appears. Click the Traceability smart button to see the updated Traceability Report, which includes a Reference document, the Product being traced, the Date, and the Lot/Serial # assigned.
The Traceability Report can also include a Reference receipt from the previous purchase order, if the product quantities shared the same lot number.
Manage lots for different operations types¶
In Odoo, the creation of new lots is only allowed upon receiving products from a purchase order, by default. Existing lot numbers cannot be used.
For sales orders, the opposite is true: new lot numbers cannot be created on the delivery order, only existing lot numbers can be used.
To change the ability to use new (or existing) lot numbers on any operation type, go to the Operation Type.
, and select the desiredFor Receipts, found on the page, the Use Existing Lots/Serial Numbers option can be enabled, by clicking Edit, and then clicking the checkbox beside the Use Existing Lots/Serial Numbers option (in the Traceability section). Lastly, click the Save button to save the changes.
For Delivery Orders, the Create New Lots/Serial Numbers option can be enabled, by clicking Edit, and clicking the checkbox beside the Create New Lots/Serial Numbers option. Be sure to click the Save button to save all changes.
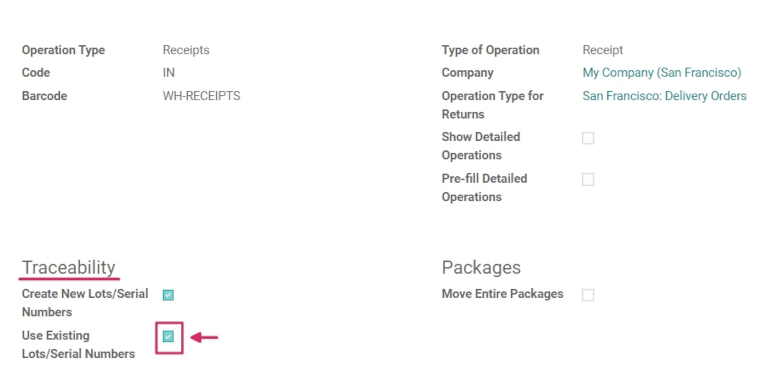
Tip
For inter-warehouse transfers involving products tracked by lots, it can be useful to enable the Use Existing Lots/Serial Numbers option for warehouse receipts.
Lots traceability¶
Manufacturers and companies can refer to traceability reports to see the entire lifecycle of a product: where (and when) it came from, where it was stored, and who (and when) it went to.
To see the full traceability of a product, or group by lots, go to the
. Doing so reveals the dashboard.From here, products with lot numbers assigned to them will be listed by default, and can be expanded to show the lot numbers those products have assigned to them.
To group by lots (or serial numbers), begin by removing any filters in the search bar. Then, click the Group By drop-down, select Add Custom Group, and select Lot/Serial Number from the drop-down menu. Then, click Apply.
Doing so displays all existing lots and serial numbers, and can be expanded to show all quantities of products with that assigned number.
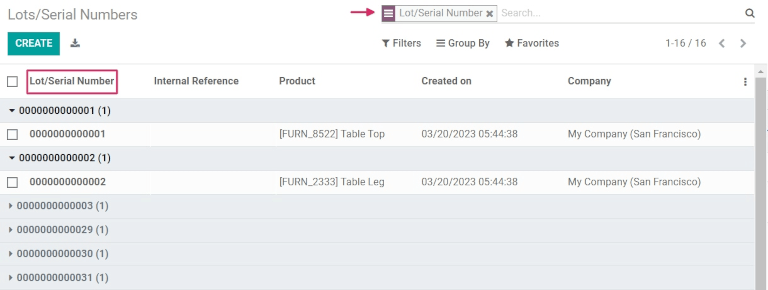