Manufacturing backorders¶
In some cases, the full quantity of a manufacturing order cannot be produced immediately. When this happens, Odoo Manufacturing allows for the manufacturing of partial quantities of the order and creates a backorder for the remaining amount.
In the Manufacturing app, creating a backorder splits the original manufacturing order into two orders. The reference tag for each order is the tag used for the original order, followed by a hyphen and then an additional number to indicate that it’s a backorder.
Example
A company creates a manufacturing order with the reference tag WH/MO/00175, for 10 units of Product X. After starting work on the manufacturing order, the employee working the production line realizes there are only enough components in stock to produce five units of the product.
Instead of waiting for additional stock of the components, they manufacture five units and create a backorder for the remaining five. This splits the manufacturing order into two separate orders: WH/MO/00175-001 and WH/MO/00175-002.
Order 001 contains the five units that have been manufactured, and is immediately marked as Done. Order 002 contains the five units that still need to be manufactured and is marked as In Progress. Once the remaining components are available, the employee returns to order 002 and manufactures the remaining units before closing the order.
Create a manufacturing backorder¶
To create a backorder for part of a manufacturing order, begin by navigating to Create.
. Select a manufacturing order with a quantity of two or more or create one by clickingIf a new manufacturing order is created, select a product from the Product drop-down menu and enter a quantity of two or more in the Quantity field, then click Confirm to confirm the order.
After manufacturing the quantity that is being produced immediately, enter that number in the Quantity field at the top of the manufacturing order.
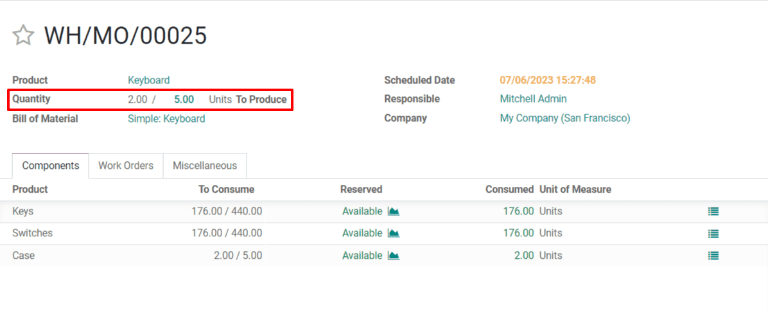
Next, click Validate, and a You produced less than initial demand pop-up window appears, from which a backorder can be created. Click Create Backorder to split the manufacturing order into two separate orders, with the reference tags WH/MO/XXXXX-001 and WH/MO/XXXXX-002.
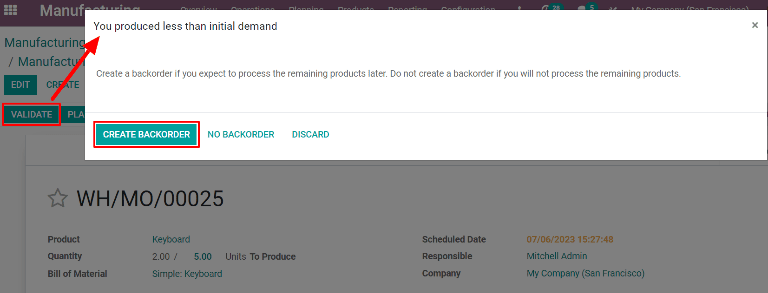
Order 001 contains the items that have been manufactured, and is closed immediately. Order 002 is the backorder that contains the items that have yet to be manufactured, and remains open, to be completed at a later date.
Once the remaining units can be manufactured, navigate to Validate to close the order.
, and then select the backorder manufacturing order. If all of the remaining units are manufactured immediately, simply clickIf only some of the remaining units are manufactured immediately, create another backorder for the remainder by following the steps detailed in this section.
Create a backorder in Shop Floor¶
Backorders for manufacturing orders can also be created from the Shop Floor module.
Note
In order to use the Shop Floor module, the Work Orders setting must be enabled. To do so, navigate to Work Orders checkbox, and then click Save.
, enable theTo create a backorder from the Shop Floor module, begin by navigating to
. Select an MO for multiple units of a product, for which a backorder needs to be created.On the MO, select the Work Orders tab, and then click the Open Work Order (external link icon) button on the line of the work order to be processed. On the resulting Work Orders pop-up window, click the Open Shop Floor button to open the Shop Floor module.
When accessed from a specific work order, the Shop Floor module opens to the page for the work center where the order is configured to be processed, and isolates the work order’s card so that no other cards are shown.
Complete the steps on the work order’s card until the Register Production step is reached, and then click on it to open the Register Production pop-up window.
Important
Do not click the # Units button on the right side of the step. Doing so automatically registers the full amount of units as having been produced.
On the Register Production pop-up window, enter the number of units produced in the Quantity field. Make sure the number entered is less than the number of units listed to the right of the field. Then, click Validate.
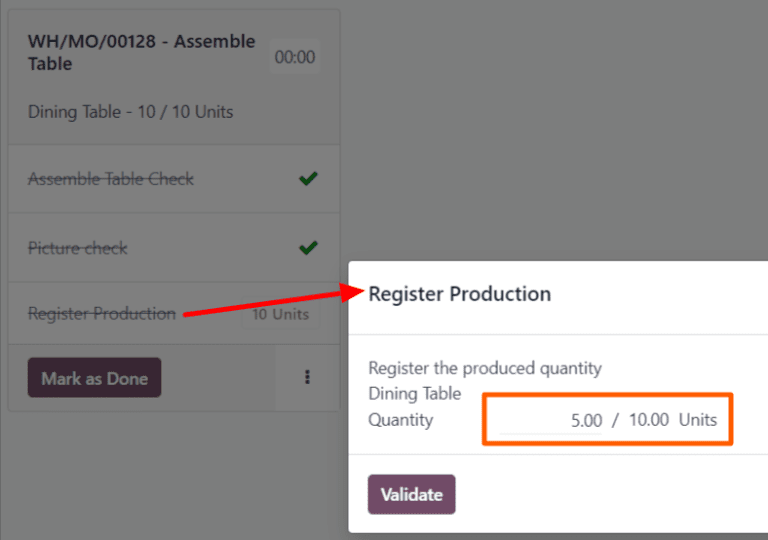
The pop-up window disappears and the # Units button on the work order’s card updates to reflect the number of units produced, as a fraction of the number of units for which the MO was originally created.
Next, click the Mark as Done button at the bottom-right of the work order’s card. The
work order card begins to fade away. Once it disappears completely, a new work order card appears,
titled with the original MO’s reference number with a -002
tag added to the end of it.
This new reference number represents the backorder MO. The original MO’s reference number now
appears with a -001
tag added to the end of it to distinguish it from the backorder MO.
If the original MO has no remaining work orders, it can be closed by selecting the All filter in the top navigation of the Shop Floor module, and then clicking Close Production at the bottom of the MO’s card.
If the original MO has remaining work orders that must be completed before it can be closed, cards for these work orders appear on the Shop Floor pages for the work centers where they are configured to be carried out. They can be processed as normal, and additional backorders can be created from their work order cards using the instructions detailed in this section.
Once the current work order for the backorder MO is ready to be processed, this can also be completed as normal, and an additional backorder can be created from its work order card by following the instructions detailed in this section.
After the final work order for the backorder MO has been completed, the MO can be closed by clicking the Close Production button at the bottom of the work order’s card.